Visit UCR Return to Campus website - Take the COVID Screening Check survey
Colloquium: Frank Abdi
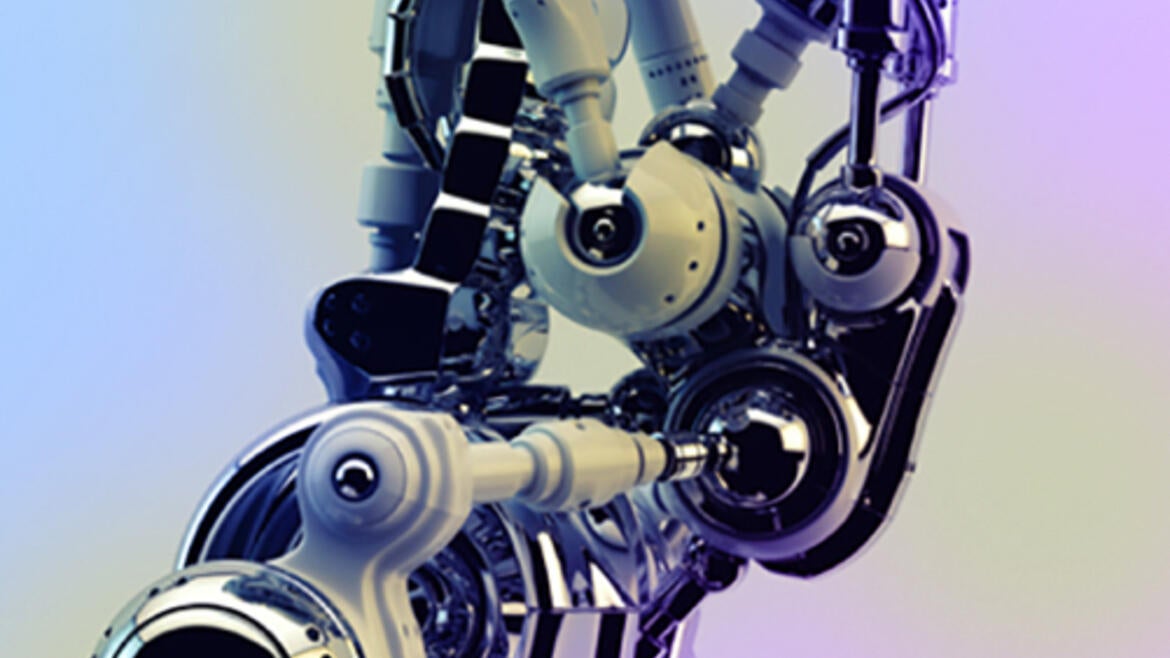
Material Characterization and Qualification of Ceramic Matrix Composites, and Nano Composite
Dr. Frank Abdi
Chief Scientist
Alpha STAR Corporation
Long Beach, California
The continuous drive to reduce advanced material development costs and time has led to the development of Virtual Testing (VT) technology which is reducing physical test requirements, guide testing, thereby reducing material qualification and certification cost. Virtual Testing utilizes a suite of software tools that handle material modeling, damage evolution and probabilistic risk analysis/optimization in advanced materials such ceramic matrix composites (CMC) or nano composite. In addition, virtual testing provides capabilities not readily available with physical testing such as the integration of uncertainties in material, manufacturing and service environments into the material design/fabrication process.
Ceramic Matrix composite (CMC) modeling requires analytical consideration of:
- Material characterization and uncertainty analysis -including Modeling of design parameters (i.e., 2-D/3-D fiber architectures, interphase, thickness effect),
- Fabrication variables and manufacturing anomalies: voids shape/size, location,
- Material performance in service: Environmental degradation, micro-crack density, and establishment of allowables,
- Damage/fracture evolution: initiation and growth, delamination,
- Material inspection and certification interval
Nano Composite improves interlamina shear and tension using nano-particles in matrix or nano tube with fiber reinforced composites. Small weight % of nano-particles significantly improves the delamination resistance. Analyzing multi-scale composites is a challenging issue, requiring analysts to consider the mechanics from nano-scale to macro-scale. Small weight % of nano-particles significantly improves the delamination resistance. The approach developed combines analytical and numerical analyses with progressive failure analysis to characterize/simulate the multi-scale composites and structural components.
General computational capabilities are summarized below:
- Assessment of delamination (ILS/ILT) improvement
- Determination of Electrical Conductivities and Thermal Conductivities:
- Prediction of impact foot print
- CNT Pull out test Prediction: to quantify interphase properties between nano particles and matrix will demonstrate the fracture energy (G2C), including Van-der-Waals effect.
The seminar will describe the technical approach followed by validation examples from life prediction software “GENOA” (1999 NASA software of the year, 2000 R&D Technology Top 100, and 2001 US Senate-SBA Tibbets, Columbia Accident Investigation awards). The software performs Multi-scale, and multi-physics material characterization, Durability and Damage Tolerance (D&DT), reliability assessments to determine multi-site failure locations, modes of failure, and provides guidelines for the development of and certification. The software has been utilized and verified by the Aerospace industry for extended ranges of ceramic and nano materials.
Dr. Frank Abdi is the chief scientist of Alpha STAR Corporation and has an extensive knowledge of the various aerospace Industry software
packages providing detailed evaluation and technical guidance for the methods being proposed for analysis of low/high temperature composite structures. Dr. Abdi has a strong theoretical and experimental background in structural materials technology including the derivation and modification of: Theoretical equations, aero-elastic tailoring (composite tapering), optimization, material design, fatigue, creep, fracture mechanics, structural mechanics, analysis of structures, and use of computers to implement these techniques.
Dr. Abdi worked at Rockwell International for fifteen years where he was the manager of Advanced Program’s Controlled Configured Vehicle Research organization. Dr. Abdi has over thirty years experience in computer based modeling and code development for a range of applications associated with advanced structures, material processing and composite mechanics with a unique background in finite difference and finite element as applied to aerospace components in support of Rockwell's division. While at Rockwell he was responsible for design and simulation of: NASP (X30), B1-B bird strike, Advanced Launch System (ALS), Boosted Penetrator, Swedish Fighter, Special Operation Aircraft (SOA), and shuttle redesign. Within Alpha STAR he has been responsible for advanced composite evaluations: High Speed Civil Transport (HSCT) Advanced Composite Technology durability and damage tolerance wing program, Aero-elastic concept engineering (ACE), Shuttle accident investigation, and several NASA/DOD/DOE sponsored composite computational structural mechanics (CSM) projects. He has the affiliation with the following professional organizations: American Society of Mechanical Engineers, AIAA (member of Optimization Committee), AIAA (member of Adaptive Structure Committee), NASA Ames (Committee in Aircraft Conceptual Design), and SAE (member of RMS Committee), Mil hand book Ceramic Committee. He has published over 100 journal papers in optimization, materials science and computational structur-al analysis, co-authored several book chapters in process optimization, Durability and damage Tolerance (D7DT), certification by analysis, virtual testing, and risk management of composite. Dr. Abdi received a B.S. and a M.S. in Mechanical Engineering from University of Michigan in 1974 and 1975 respectively, and a Ph.D. in Mechanical Engineering from University of Southern California in 1979. He also serves as visiting invited professor at Imperial College of London Department of Mechanical engineering.